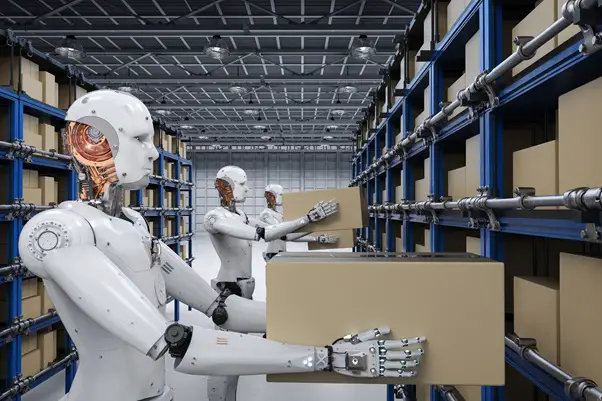
UPS drivers almost never turn left and you probably shouldn’t either. And that’s not because their CEO is superstitious. With the help of artificial intelligence, they’ve calculated that turning left costs their company 10 million gallons of fuel more and 20,000 tonnes of carbon dioxide more compared to going right or straight. Today, the company delivers 350,000 parcels more annually and has reduced the fleet’s distance traveled by 28,5 million miles. And this happened because of the power of artificial intelligence.
Among multiple examples illustrating how artificial intelligence is revolutionizing societies, the logistics industry is one of the pioneers. The reason is simple – logistics management software development brings business operations completely to a new level, optimizing delivery processes, warehouse management, analytics, automation, and customer experience.
Robo-workforce marching in the warehouses, customers receiving personalized offers based on their location, preferences, and search history, route optimization, and smart sensors sending warnings to inventory managers are just a few of the examples of how AI is turning traditional logistics upside down.
3 Main Ways AI is Transforming Logistics
Warehouse Management
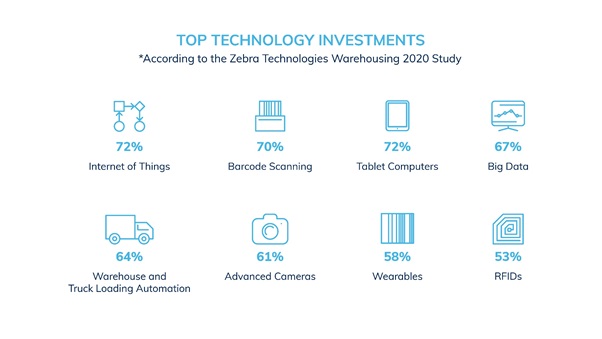
Artificial Intelligence optimizes the majority of manual tasks within warehouses. Sensor devices and actuators that contain RFID tags and scanners are able to collect data, store it in the cloud, analyze it, and provide data-driven predictions. AI devices also control the temperature, humidity level, and atmospheric pressure to eliminate the risk of goods damage or spoilage. They also significantly reduce downtime and equipment repair costs due to the ability to detect malfunctions at the early stages.
Sensors track the location and quantity of all items inside the warehouse from the point of their arrival to the moment they leave it. Therefore, inventory managers receive immediate notifications if any item is out of stock or stored in the wrong place and under inappropriate conditions. Besides data manipulations, robots perform all routine tasks such as sorting, lifting, and packing the goods, reducing the need for a large number of employees and minimizing the possibility of human error.
Amazon Robotics’ Kiva robots, for instance, are able to lift up to 750 pounds and find the directions by reading the barcodes on the ground. Today, there are more than 200,000 robots in operations within Amazon warehouses in the US that significantly optimize inventory storage and shipment. They also announced the upcoming introduction of two new robots – Ernie and Bert – that will move heavier items, navigate facilities independently, ensuring a safer work environment for employees.
According to Morgan Stanley, in 2022, due to its increased automation, Amazon will ship 6,5 billion packages, becoming a major threat for UPS, USPS, and FedEx.
Power of Big Data

The application of artificial intelligence unlocks the great potential of big data in logistics that allows the collection and analysis of high volumes of structured and unstructured data. The companies get the ability to make data-based decisions and optimize their performance using the power of big data and advanced analytics. The information is collected from business forecasts, vehicle diagnostics, advertising, social media. website, and many other resources and then thoroughly analyzed by AI. On the basis of this analysis, companies can find out about inefficiencies in their logistics supply chain, receive better transparency in their business operation, and address a range of challenges connected with last-mile shipping, route optimization, sensitive goods delivery, and warehouse automation.
One of the largest and most trusted global shipping companies, UPS, with the help of big data analytics has found out that trucks that turned left were more likely to get stuck in traffic jams, therefore, consumed more fuel and provoked a growing number of delays. The company has managed to build routes in such a way that now all trucks go straight or turn right in 90% of cases. Such a strategy saves UPS 10 million gallons of fuel, increases the delivery rate to 350,000 more packages per year, and averts emissions equivalent to more than 20,000 cars.
Customer Experience
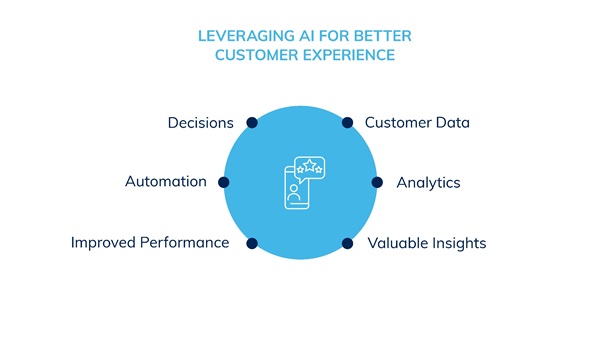
The majority of clients have only two touchpoints with logistic companies – when they checkout with e-commerce retailers and when they receive a parcel or return it. While with businesses we have a completely different picture – they need to sign long-term contracts, arrange service level agreements, and proper operation of global supply chains. According to a survey held by Gartner, 42% of customers in the US and EU said that the experience they had with a company is more important than the price of the item they bought, while Oracle’s study has shown that 90% of US customers stopped using services of the company with which they had poor customer experience. As a result, logistics companies actively apply artificial intelligence into their customer-related services to clinch a good deal and personalize each of the aforementioned touchpoints. E-commerce websites, for example, offer their customers personalized recommendations based on their search history, purchasing behavior, age, sex, and even weather conditions in their country. Instead of employees who are available only during their working shifts, chatbots answer clients’ questions 24/7 and help them choose the item that fits their requirements the best. Intelligent supply chain management software analyzes thousands of external data sources to monitor and predict possible delays in transportation because of weather conditions, traffic congestions, etc.
DHL Parcel, for instance, has expanded its customer service with Amazon’s smart speaker Alexa. By activating Alexa’s DHL Parcel function, customers can receive information about shipment details immediately and at any time.
We’re on the cusp of artificial intelligence transforming logistics. Logistic companies are actively trying to take the innovation by storm to remain competitive, optimize their warehouse management, bring transparency to the supply chain, protect their goods, and optimize transportation. Customers, in return, are demanding more personalized, swift, and pleasant experiences. According to Accenture, 36% of small-, mid-, and large-size companies have already adopted AI for logistics and supply chain operations, and more are to come. Today innovation is a norm not an option and AI promising a plethora of opportunities to exploit is one of its central tenets.