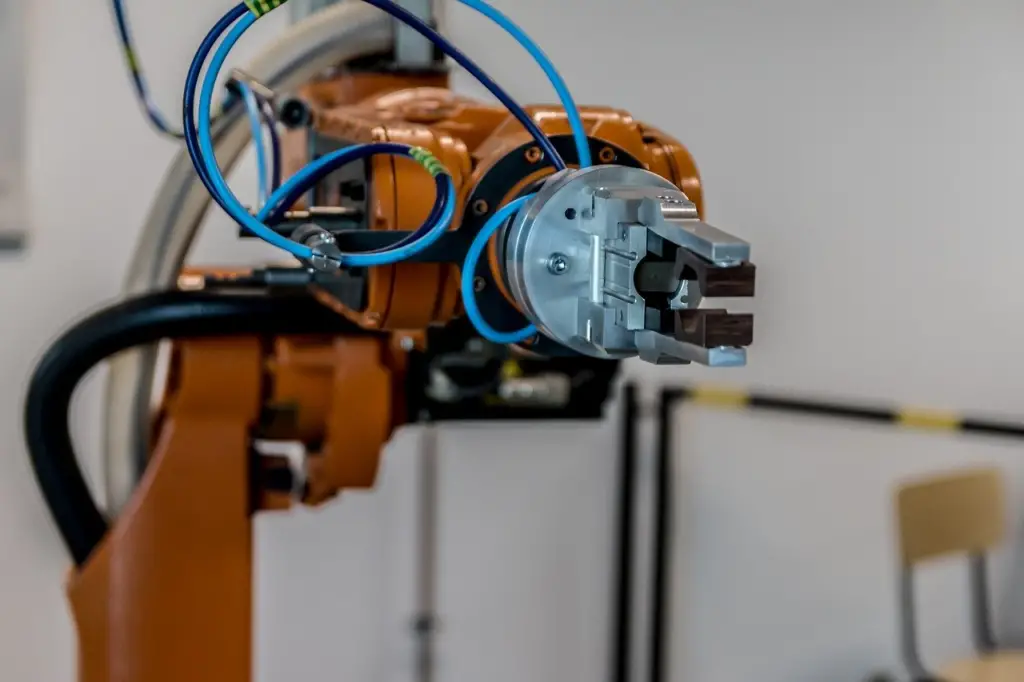
Collaborative robots are designed mostly for machine tending. A cobot can work beside a person safely because it contains safety features installed in it. Hence, it can work collaboratively you’re your workers on the production floor to perform certain tasks without barricading it.
Getting the cobot on the floor and programming it to load and unload parts isn’t a walk in the park. To begin with, you must choose your cobot carefully and ensure that it can perform tasks like a person.
Choosing the Right Collaborative Robot for Your Machine Tending Needs
Here are a few factors to take into consideration when choosing the right cobot for your robotic machine tending needs.
Specifications
- Maximum Payload
Payload refers to the total weight the cobot can take. Weigh your tool against the bulkiest raw part you need to be carried to determine the payload.
- Repeatability
Your cobot does not have to be as precise as your machines. In many factories, the cobot performs the first setups with a part that is usually bigger than the end product. This gives some space for minor deviations while positioning the part.
- The Cobot’s Reach
The robot must pick a part from one place in order to place it in the machine. To get the minimum reach of your robot, measure the distance between the two places, and then divide that by two. The reach includes the number of axes that your robot’s arm has.
Gripper Specifications
- Stroke
The gripper is the one that grabs the part to put into the machine. Simply put, it is the robot’s hand. However, it does not work as well as a human hand.
To work properly, your robot’s gripper must have two parallel surfaces at least. The gripper’s stroke lessens the scope of the part to be handled. You must measure your largest part to make sure that you purchase the gripper that will suit the part.
Opt for an adoptive gripper that is designed to handle different shapes and sizes of parts. It should be able to do this without altering either its fingers or the robot program. Also, ensure that it can grip 85% to 95% of the parts.
- Payload
The gripper should be able to comfortably handle the weight of your largest part. Make sure you adhere to this for your gripper to last long.
Adequate Workspace
- The Machine Interface
The interface between your cobot and the machine is significant in machine tending. Given that different manufacturers produce machines with varying features, you must make the best of your cycle time.
Your machines must be able to ‘communicate’ so that each is aware of the status of the other. The communication between the two machines has to do with the following states:
- The program is done
- The door can be opened
- The robot is running
- The vice is closed
- The part is in place
Your cobot and machine should share a common interface. Some robot models may not be on the same page with the machine with regard to communication. Do not attempt to program the robot with a timer.
- Ordering Devices
These are the devices used to command the picking and placing of parts in an orderly manner. Robotics experts recommend the addition of a basic device that positions the part in the same place every time. This helps to make programming easier as well as highly repeatable.
- Vice
An automated application requires an automatic vice. Purchase one from your tool providers if they stock them.
- Door
Collaborative robots are programmed to open doors and close them. Reduce your cycle time by integrating small air cylinders to be managed by the cobot.
Conclusion
For your robotic machine tending to work to your expectations, you must be able to purchase the right collaborative robot. Always get more insights from robotics experts to get the right cobot for your specific needs.