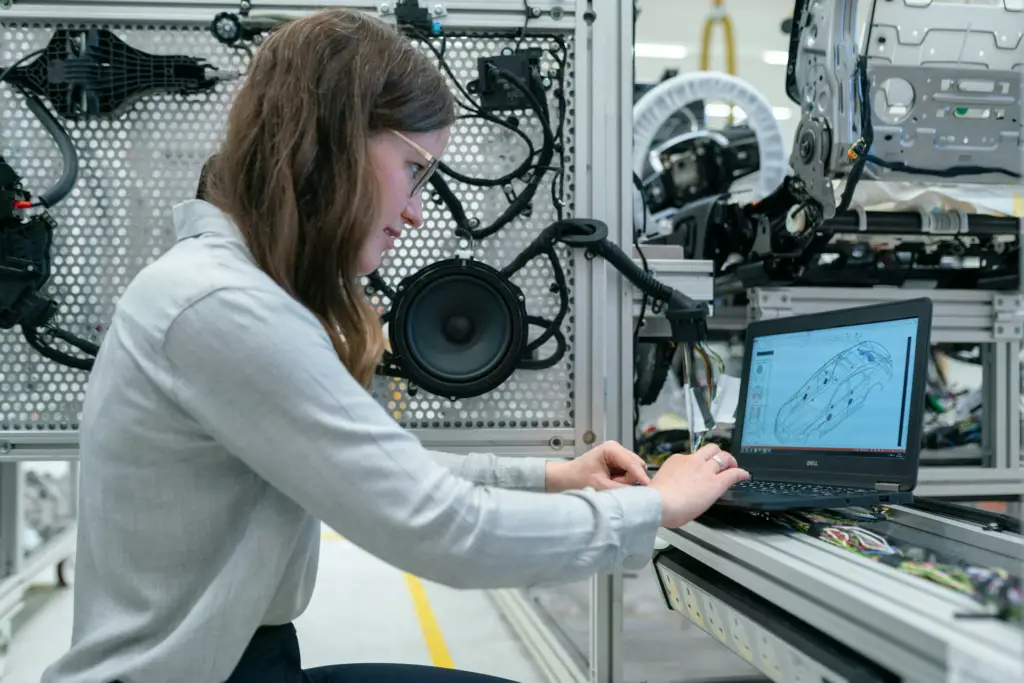
The manufacturing industry is currently experiencing a transformation, which brings opportunities to boost efficiency and productivity. A key player in this transformation is software. This innovative technology allows manufacturers to create replicas or “twins” of their assets and processes, enabling them to gather valuable insights and make data-informed decisions to enhance their operations. This post will delve into how digital twin software is transforming manufacturing processes and optimizing efficiency.
I. Understanding Digital Twin Software
Digital twin software generates a copy of physical assets or processes within a simulated environment. This cutting-edge technology produces a model by integrating data from sensors and machines with real-time analytics. By replicating assets intricately, manufacturers can attain improved visibility into their operations, facilitating decision-making.
II. Enhancing Efficiency via Simulation
A benefit of digital twin software is the capacity to simulate various scenarios before implementing them physically. Manufacturers can virtually test configurations, factors, and variables without disrupting activities or risking costly mistakes.
For instance, a manufacturing facility could utilize software to simulate alterations in production line layouts or equipment settings before applying them on-site.
By examining these simulations in advance, managers can pinpoint bottlenecks or inefficiencies and create plans to address them. Using the forecasts derived from the simulation outcomes, plant supervisors can make informed choices based on current information rather than solely depending on gut feelings or guesswork.
III. Enhanced Production through Predictive Maintenance
Unscheduled equipment downtime can have an impact on productivity and costs within manufacturing facilities. Digital twin technology equips manufacturers with the capability to anticipate machinery failures by analyzing sensor data and historical records.
By incorporating machine learning algorithms into the system, indications of potential equipment breakdowns can be spotted early, even before they are noticeable to human operators. This proactive maintenance approach enables manufacturers to plan repairs or replacements during scheduled maintenance periods, reducing downtime and minimizing production disruptions. Ultimately, proactive maintenance results in cost savings and prevents unnecessary interruptions in production processes.
Moreover, digital twin software aids in enhancing the equipment efficiency (OEE) metric, a performance measure for gauging productivity levels. By monitoring factors such as availability, performance, and quality through data inputted into the model, manufacturers can pinpoint areas that are underperforming and swiftly implement corrective measures to optimize their operations.
IV. Continuous Improvement through Real-time Data Analysis
In the fast-paced world of manufacturing today, staying ahead means looking for ways to improve and adapt. Digital twin technology analyzes real-time data collected from sources on the factory floor.
Manufacturers can quickly identify trends or irregularities that need addressing by gathering and examining data streams from sensors and machinery within a twin framework. This enables them to respond promptly to any performance or quality levels changes in their operations.
Furthermore, tapping into data stored in the system allows manufacturers to analyze past operational trends. By combining this knowledge with real-time simulations, they can pinpoint areas for optimization while considering factors like inventory management, workforce distribution, and supplier lead times.
V. Harnessing Insights for Enhanced Process Efficiency
Digital technology equips manufacturers with insights that drive significant process improvements. With features such as simulation modeling and predictive analytics, many companies have already seen enhancements across aspects of their business:
1. Resource Management:
Digital twins visualize resource usage, helping identify energy inefficiencies and material wastage for better resource allocation.
2. Operational Efficiency:
Simulation models uncover operational bottlenecks and inefficiencies, guiding adjustments that enhance efficiency.
3. Workforce Productivity:
By examining how resources are distributed based on records and hypothetical situations, manufacturers can enhance productivity.
4. Quality Control:
Continuous monitoring identifies deviations promptly, allowing for actions to prevent defects and enhance product quality.
Conclusion
The utilization of technology offers an innovative and compelling solution for manufacturers aiming to streamline their operations, improve efficiency, and drive profitability. By creating replicas of physical assets and utilizing real-time data and analytics, companies can make informed decisions, enhance maintenance practices, boost productivity, and uncover avenues for enhancement.
As the manufacturing industry evolves rapidly, the adoption of technology becomes increasingly crucial. It empowers manufacturers to adapt swiftly to changing market demands, outperform competitors, and succeed in the era of transformation. With advancements in features and capabilities, digital twin software shows potential for revolutionizing manufacturing processes globally.