Electric vehicles (EVs) are set to alter the global automotive landscape. With a growing demand for such cars, manufacturers are seeking specialized components. They want efficient, high-performing, lightweight components for such vehicles. Powder metallurgy technology plays a pivotal part in EV manufacturing. Let us see how the powder metallurgy process is critical in the EV sector.
Why is powder metallurgy suitable for EVs?
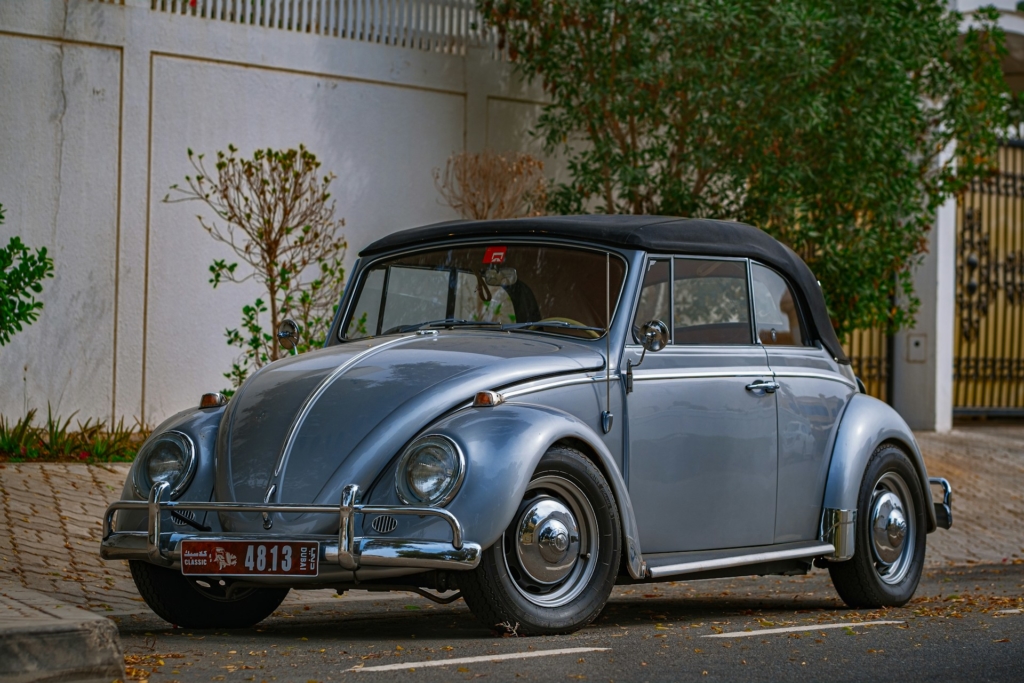
Electric vehicles have unique usage cases, and those definitely need innovative solutions. EV components should be lightweight and sturdy. This is necessary to offset their heavy battery systems. They have to be wear-resistant and sturdy, along with having top-notch electrical and thermal properties.
Powder metallurgy fits the bill for all these areas. The PM process offers high-performance automotive components with minimal waste, and it is becoming a favorite in EV manufacturing.
3 Things You Need to Know Before Buying an Electric Vehicle — Not After
How is powder metallurgy used in EV making?
Some of the ways are discussed below:
- Battery cooling systems–Powder metallurgy is used to make the components with customized, required porosity. These are used to make heat exchangers and cooling plates for EV battery packs.
- Braking system–EVs are typically equipped with regenerative braking systems for better mileage. PM-derived components like brake pads and rotors have good thermal stability. These also offer excellent wear resistance.
- Lightweight, structural parts–EV batteries weigh a lot. So, automakers prefer using lightweight powder metallurgy parts. This helps them reduce overall vehicle mass. Structural PM components like brackets and housing offer the required weight reduction and strength mix.
- Drivetrain components–EV drivetrains require durable and lightweight parts for optimal power delivery. Powder metallurgy-made rotor and stator cores, gears, and parts fit the bill.
Things No-One Tells You About Owning An Electric Vehicle
Core Benefits of powder metallurgy in EV manufacturing
Let’s have a look at the core benefits of using PM in EV making:
- Material efficiency–PM technology is sustainable with minimum material waste. It is cost-effective, aligning with the sustainability goals of EV brands.
- Design freedom – PM offers superb flexibility in creating EV components with complex designs. Examples are specialized battery connectors and motor housings.
- Mass production within budget– EVs have become mainstream in many countries. The PM components offer flexible solutions without sacrificing quality or performance.
- Custom material properties– PM parts usage leads to better thermal conductivity or excellent magnetic permeability for the EV systems.
Hurdles resolved by powder metallurgy in EVs
Common hurdles resolved include:
- Heat management–EV batteries can create a lot of heat. Diverse PM parts offer superior thermal properties, helping in heat management.
- Magnetic motor performance– Soft magnetic composites made by the PM process help improve motor performance and reduce energy loss.
- Noise, vibration, and harshness (NVH)–EVs run quietly when fitted with PM parts, which help minimize NVH.
Electric Car Charger Installation: What Homeowners Should Know
Summing it up
Powder metallurgy has helped usher in an unforeseen transformation in the electric vehicle sector. PM offers better energy efficiency, reliable performance, and superb sustainability– factors deemed necessary by EV manufacturers. From making lightweight and sturdy parts to developing efficient motor components, powder metallurgy holds the key to the growth of the automotive sector.