In robotically-dominated industries, precision and dependability are more than mere dreams; they are definite needs. This is because, for robotics, sensors are like eyes that help the system sense the environment, interpret data, and interact with it, whereas photodiodes are one of the most significant sensor components.
Photodiodes are elements in the sensing systems that turn light into electric signals, and applications such as LiDAR, optical encoders, and proximity sensors, among others, are indispensable. However, this kind of device must undergo rigorous tests to ensure that it meets elevated robotic systems standards.
Let’s discuss further why laser diode testing is very important in robotics, the kinds of tests that need to be carried out and how leading companies like Electron Test Equipment are enabling breakthroughs in this field.
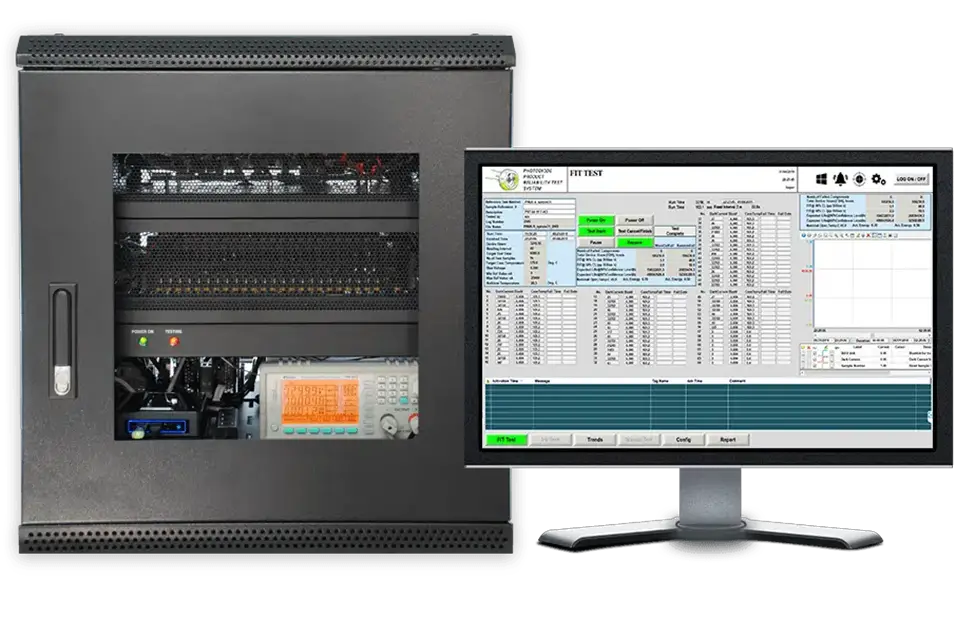
Why is Laser Testing Critical in Robotics?
Photodiodes are robots’ eyes because they enable them to sense light, measure distances, and perform any kind of optical work with great accuracy. Still, even minor deficiencies in photodiode outputs can cause significant problems, such as inadequate navigation errors during LiDAR operation.
For Instance, In LiDAR applications, inaccuracies in distance measurements due to photodiode errors can lead to navigation failures or collisions, emphasizing the critical need for accurate testing.
– Poor Responsiveness: Photodiodes used in proximity sensors must quickly and accurately detect changes in light levels. Slow response times or signal noise can compromise a robot’s real-time ability to react.
Photodiodes in optical encoders play a crucial role in detecting light interruptions to measure motion. However, subpar photodiodes can lead to miscalculations in positioning or speed control, directly impacting the robot’s overall efficiency.
Comprehensive testing is crucial to ensure that photodiodes perform consistently and reliably, reducing the risk of system crashes during use.
Types of Photodiode Testing Required in Robotics
The testing of photodiodes for robots requires several key assessments, each aimed at establishing certain operational aspects:
Responsivity Testing
The testing involves exposing the photodiode to different wavelengths and light intensities and ensuring that it performs consistently over an operational range. The test on how well a light sensor transforms light energy into an electrical signal whenever there is a lack of consistency in terms of darkness or brightness, as observed in robotics, would be imperative here.
Linearity Testing
Another important parameter for any photodiode is its linearity, which implies that the current generated should be proportional to the intensity of light falling on it. This feature requires precision data interpretation, especially in LiDAR applications, where precise distance measurement involves accurate light measurements.
Noise Testing
This includes looking out for electrical noise that may interfere with the diode’s output, thereby leading to wrong readings. Noise analysis intends to ascertain the reliable performance under dynamic environments with respect to the signal-to-noise ratio.
Dark Current Testing
Dark current, a relatively small amount of charge that flows through a diode even when no light falls on it, is a crucial factor in photodiode performance. Too much dark current can diminish sensitivity while also increasing power consumption, both of which are harmful to robots. Therefore, during testing, the amount of dark current is checked to ensure it is within a reasonable range, thereby maintaining the sensitivity and power efficiency of the photodiode.
Stability and Reliability Testing
Robots operate in places with highly fluctuating temperatures and humidity and may thus be exposed to vibration. This justifies why endurance tests are performed on these devices since they always remain in use under such conditions.
Automated Test Equipment: A Key Enabler
Manual photodiode testing processes cannot be used in complex ways due to their complexity and the accuracy demanded by such devices. Automated test equipment (ATE) is the solution for efficient high-scale evaluations of photodiodes. Companies such as Electron Test Equipment offer ATE systems that have high-throughput testing repeated with unmatched accuracy.
Key Features of Automated Testing Systems:
– High Precision: Automated systems can measure tiny variations in photodiode performance, ensuring consistency across batches.
– Parallel Testing: Multiple photodiodes can be tested simultaneously, reducing time-to-market for robotics manufacturers.
– Customizable Parameters: Engineers can configure tests to mimic specific operating conditions, making the results highly relevant to real-world applications.
– Comprehensive Reporting: Detailed test data allows for better quality control and performance analysis.
Leading Companies in Photodiode Testing for Robotics
1. Electron Test Equipment
Electron Test Equipment excels in automated photodiode and semiconductor testing. Some unique aspects of this company’s Automated Test Equipment includes parallel testing capabilities and customized test protocols meant for robotics applications alone. They are considered highly dependable because various manufacturers, from the mobile robotics sector to the electronics sector, rely on them for accuracy and reliability.
2. Teradyne
Teradyne is a leader in providing comprehensive semiconductor and photodiode testing solutions using advanced ATE. To meet the demands of the robot industry, their equipment is designed to be scalable and is often being sold under different names.
3. Advantest
They offer automated test solutions that generate detailed photodiode performance data. This is why, in robotics, where accuracy is not negotiable, they are often found keeping up with their peers in quality.