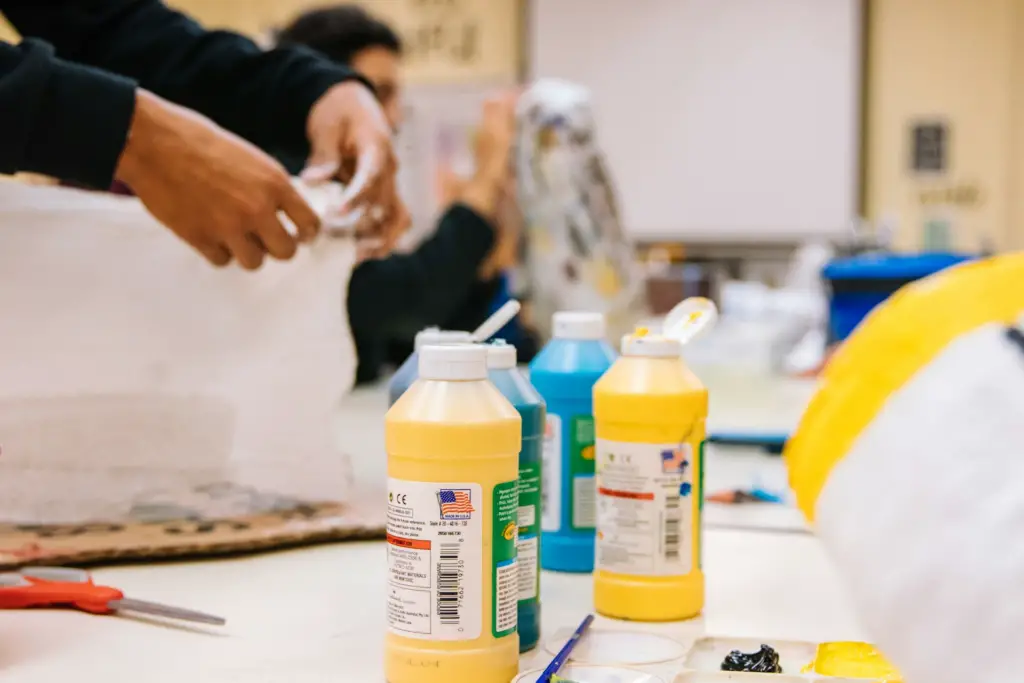
In today’s manufacturing industry, the importance of having a well-trained and knowledgeable workforce cannot be overstated. However, training workforces can be an endeavor without the right tools and strategies in place. This is where Learning Management Systems (LMS) step in. This article delves into how LMS is transforming training in the manufacturing sector by streamlining processes and enhancing employee skills.
From onboarding hires to upskilling existing employees, LMS offers organizations a comprehensive solution to optimize their training programs efficiently. Thus, make an informed decision by looking at LMSs by reputed SaaS providers. While doing so, ensure to look at their insights, features, and pricing. For example, if you select Blackbaud, look at Blackbaud’s pricing, reviews, and other information.
Streamlining Onboarding Process
1. Efficient Training for New Hires
Utilizing LMS manufacturing, companies can develop onboarding programs that simplify the training process for hires. Employees can conveniently access information about company policies, procedures, and safety protocols through modules, videos, and quizzes. LMS enables the automation of tasks like course assignments and progress tracking, allowing trainers to allocate time to crucial aspects of onboarding.
2. Ensuring Consistent Training
With LMS implementation, manufacturers ensure training across shifts or locations.
By consolidating training resources on the platform, all staff members gain access to knowledge crucial for their effective performance in their respective roles. This consistency reduces errors and minimizes the likelihood of accidents stemming from inconsistent training practices across different teams.
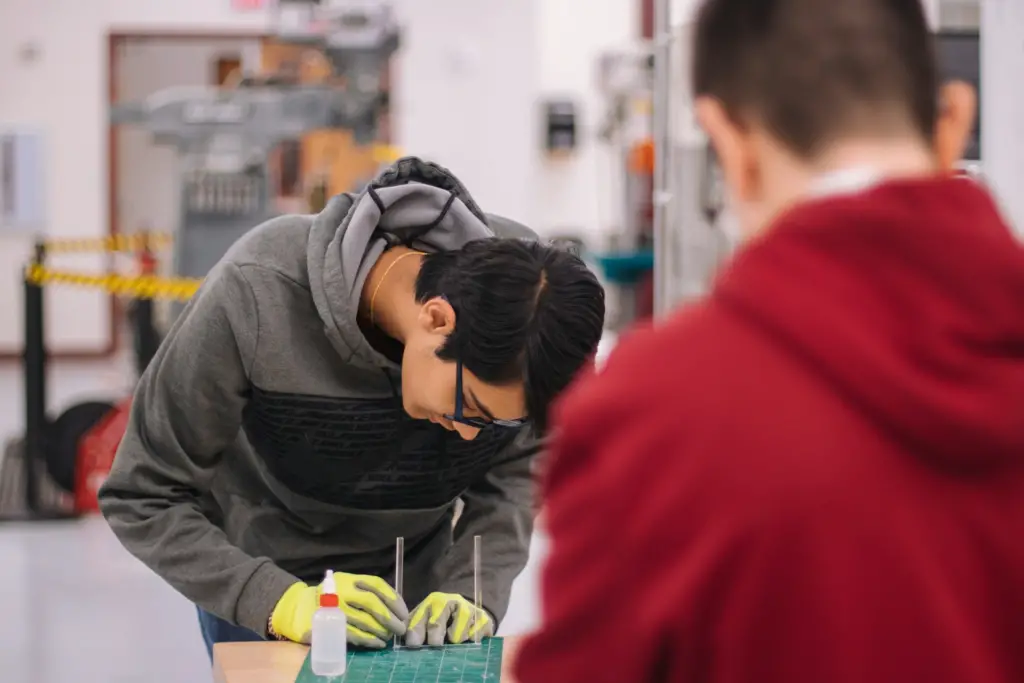
Enhancing Workforce Skills
1. Continuous Learning Opportunities
Manufacturing processes constantly evolve due to advancements and changes in regulations.
An LMS provides a platform for delivering training related to these updates. Employees can conveniently access updated content anytime and anywhere, enabling them to stay well-informed about industry trends and best practices without disrupting production schedules.
2. Training Programs
Given the range of roles within manufacturing organizations, it is not necessary for every employee to receive identical training materials. An LMS offers customization options so that each employee receives course material tailored to their job responsibilities. Managers can even. Analyze employee performance to identify areas where additional knowledge is needed, allowing for training interventions.
Workplace Safety
1. Safety Training
In the manufacturing sector, workplace safety is of importance. LMS platforms enable companies to deliver safety training to all employees. Interactive modules, simulations, and assessments assist employees in understanding hazards, preventive measures, and emergency response techniques. LMS systems can also generate reports on how many employees have completed safety training, ensuring they follow industry regulations.
2. Tracking Compliance
Compliance with regulations is crucial in the manufacturing industry, as noncompliance can lead to consequences. LMS simplifies compliance tracking by allowing documentation of certifications or licenses. Trainers can even set automated reminders for certifications that are about to expire, ensuring employees stay updated with requirements.
Improved Training Administration
1. Centralized Training Management
Managing training programs across locations or departments can be a task. With an LMS, all training materials are centralized, reducing burdens related to record-keeping and content distribution.
2. Efficient Reporting and Analytics
LMS platforms offer reporting features that provide insights into employee performance and the effectiveness of training programs. Managers can access real-time analytics and track trends such as completion rates, assessment results, and overall knowledge retention. Having access to this data enables organizations to evaluate the impact of training initiatives, identify areas for improvement, and make decisions regarding employee development.
Engaging and Interactive Learning
Traditional training methods often rely on one-way communication, making keeping employees engaged and motivated difficult. Learning Management Systems (LMS) have transformed the way workforce training is conducted in the manufacturing industry. By simplifying processes and improving outcomes, LMS has made an impact. It offers features like gamification, quizzes, and simulations that make learning enjoyable and captivating for employees. Employees can engage in real-life scenarios through labs and simulations, allowing them to apply their knowledge and skills in an environment. This active learning approach enhances knowledge retention and boosts employee engagement with the training materials.
Conclusion
In conclusion, LMS plays a role in revolutionizing workforce training for manufacturers. It facilitates onboarding experiences for hires while providing continuous learning opportunities for existing employees. With a focus on safety through the efficient delivery of safety training and centralized reporting capabilities for compliance monitoring, LMS ensures that manufacturing businesses achieve their objectives efficiently and effectively. Embracing these solutions enables manufacturers to optimize their training efforts, resulting in a well-rounded workforce.