3D printing technology has come a long way in recent years, revolutionizing various industries and opening up new possibilities. One of the most exciting advancements in this field is Selective Laser Sintering (SLS) printing. This article will explore the basics of SLS printing, its impact on manufacturing, the applications it offers and the future trends and innovations in SLS technology.
Understanding the Basics of SLS Printing
SLS printing is a type of additive manufacturing that uses a high-powered laser to fuse small particles of material together, layer by layer, to create a three-dimensional object. Unlike traditional manufacturing methods that involve cutting or drilling away material, SLS printing builds objects from scratch, resulting in less waste and more design freedom.
The process begins with a bed of powdered material, typically plastic or metal, which is spread evenly across the build platform. The laser then selectively fuses the particles based on a digital model, solidifying the desired shape. Once a layer is complete, a new layer of powder is spread and the process is repeated until the object is fully formed.
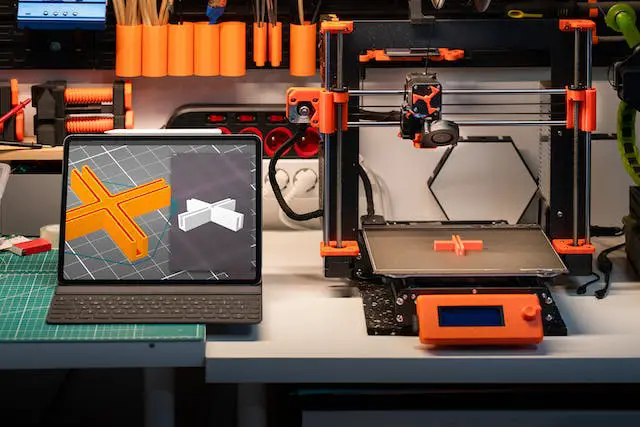
Revolutionizing Manufacturing With SLS Printing
Because SLS printing has so many advantages over conventional methods, it has the potential to revolutionize the manufacturing industry. One of the key benefits is the ability to create complex geometries that would be difficult or impossible to produce using conventional techniques. This opens up new design possibilities and allows for the creation of lightweight, high-performance parts.
Furthermore, SLS printing enables rapid prototyping, reducing the time and cost associated with traditional manufacturing processes. It also eliminates the need for tooling, as objects can be directly printed from a digital model. This makes it particularly suitable for small-scale production runs or customized products.
The Advantages of SLS Printing in Manufacturing
Here are a few advantages of using SLS printing in manufacturing:
- It enables the production of lightweight yet durable parts, making it ideal for applications in the aerospace, automotive and medical industries.
- Multiple components can be integrated into a single part using SLS printing, which speeds up assembly and enhances product performance overall.
- SLS printing supports the use of a wide range of materials, including engineering-grade thermoplastics and metal alloys, further expanding its potential applications.
Exploring the Applications of SLS Printing
SLS printing has found applications in various industries, including aerospace, automotive, healthcare and consumer goods.
- In aerospace, it is used to create lightweight components for aircraft, reducing fuel consumption and improving performance.
- In the automotive industry, SLS printing is utilized for rapid prototyping, tooling and the production of customized parts.
- In healthcare, SLS printing has been used to create patient-specific implants, prosthetics and surgical instruments. Its ability to produce complex, porous structures also makes it suitable for tissue engineering and drug delivery systems.
- SLS printing has also been employed in the production of consumer goods such as fashion accessories, home decor and electronics.
Future Trends and Innovations in SLS Technology
The future of SLS printing looks promising, with ongoing research and development focused on improving the process and expanding its capabilities. One area of innovation is the development of new materials for SLS printing, including biodegradable polymers, ceramics and metals. These advancements will further broaden the range of applications and enhance the performance of printed objects.
Another trend is the integration of SLS printing with other technologies, such as robotics and artificial intelligence. This combination allows for more efficient and automated production processes, reducing human intervention and increasing productivity. Also, advancements in software and design tools will make it easier for designers and engineers to create complex geometries and optimize the printing process.
In conclusion, SLS printing is a groundbreaking technology that is revolutionizing manufacturing across various industries. Its ability to create complex geometries, reduce waste and enable rapid prototyping makes it a valuable tool for designers and engineers. As research and development continue, further advancements in 3D printing and SLS technology are expected, thereby expanding its applications and pushing the boundaries of what is possible.