Nanotechnology is expected to be the flagbearer for the next technological revolution. Nanotechnology essentially deals with utilizing the materials and their properties at a nanometric scale. One of the most important challenges in the widespread use of nanotechnology in daily life products is associated with the manufacturing techniques and costs associated with these methods. Challenges lie in not only manufacturing parts with features at a nanometric scale but also with its integration with parts having micrometric features and macro devices.

What is nano machining?
There are two ways in which nano machining is defined. The first one describes nano machining as creating parts that have an overall dimension of nanometric scale. The second one describes it as machining processes in which precision of 100 nm or less than 100 nm must be maintained regardless of the size of the overall product. Nanometric machining can be broadly classified into four different types.
Abrasive nanometric machining
In abrasive machining, abrasive particles are used to remove small amounts of material from the surface of the part. The size of abrasive particles used determines the scale of the features to be produced. Honing, polishing, and lapping processes are included in this category.
Non-mechanical nanometric machining
These methods include micro Electric Discharge Machines (EDM) and focused ion beam machining etc.
Lithographic methods for nanometric manufacturing
Through the use of masks, two-dimensional parts, and features with precision at nanometric scales are produced. These methods are limited to creating only two-dimensional parts. Techniques include X-ray lithography, electron beam lithography, etc.
Mechanical nanometric machining
This method uses tools as in conventional mechanical machining to remove materials on a scale of tens of nanometers. Tool path and surface determine the shape and quality of the workpiece that is to be manufactured. Processes are nano grinding, micro-milling, and diamond turning.
Mechanical nanometric machining is preferred over other machining methods due to its ability to generate complex three-dimensional geometric features at different length scales. For example, mechanical nanometric machining is used to create micro molds with complex geometrical and form features at a nanometric scale.

Important physical parameters for mechanical nano machining include cutting force, cutting energy, cutting temperature, chip formation, and surface generation. These parameters provide means to understand the physical process of machining. Molecular Dynamics Simulation (MDS) is used to determine these parameters, theoretically. Critical cutting edge radius, minimum undeformed chip thickness, and properties of workpiece material also play an important role in understanding the process of machining.
Factors to consider for nano machining
For the successful implementation of the nano machining, while keeping in view the quality constraints, it is imperative to consider the following factors.
Ultra-precision machine tools
To manufacture precision parts with nanometers, it is essential to use a machine consisting of ultra-precision machine tools. As a unit, there are certain properties that must be exhibited by these ultra-precision machine tools. These properties include the high mechanical and thermal stability of the parts. Values of the natural frequency and loop stiffness of the structure must be high. As an entity, these tools must demonstrate low vibrations. Control and motion of the axis must be extremely precise.
To constitute an ultra-precision machine tool, four major systems (drive and spindle, mechanical structure, measurement system, control system) are required.
Cutting tools
The most common type of cutting tool used in nano machining consists of diamond tips. Diamond is preferred over other materials due to its properties. The advantages of using diamond-tipped tools include better thermal management due to the high thermal conductivity values of diamonds. Due to the crystalline structure of the diamond, an extremely sharp cutting edge is produced. Diamond tools are also highly wear-resistant. During machining, diamond tools exhibit reduced tool deformation owing to the high shear and elastic moduli values of the diamond. Diamond also has a high value of hardness. There are certain disadvantages associated with cutting tools, made from diamond, as well. Diamond lacks toughness and has an affinity with ferrous materials. Grinding wheels used in nano machining are often made of diamond bonded with metal.

Nano metrology
It is extremely important to have methods and techniques at our disposal that can help us determine the quality of the parts subsequent to nano machining. Measurement of dimension, form, texture, and surface integrity with high precision is necessary for effective quality control in nanometric parts.
Laser interferometers are used widely to determine the position with nanometric scale precision. Scanning probe microscope and optical profiler are extensively used for surface texture measurement.
Measuring form such as the curvature of a round surface becomes important especially for optics-related applications where departure from the perfect shape can result in failure during functional testing of the part. Interferometric techniques (i.e. phase stepping) are used to determine the conformity of the complex shapes to the original design.
Variables for nano machining processes
Intended functions that a product must perform determine the design and control processes for deciding the machining variables. Factors such as surface roughness, wear resistance, friction, lubrication, etc. play a deciding role in the selection of machining methods and parameters.
Applications of nano machining
Nano-Electro-Mechanical Systems (NEMS) are the advanced form of Micro-Electro-Mechanical Systems (MEMS). These systems integrate electrical (e.g. transistors) and mechanical (e.g. pumps and actuators) systems at the nanoscale. NEMS are famously used for accelerometers and the detection of chemicals in the air. Giant Magnetoresistance (GMR) structures for computer hard disk read head is one of the most famous applications of devices at the nanoscale.
Other applications of nano machining include the manufacturing of astronomical mirrors and other optical instruments for use in optical instruments. Nano machining is also used to machine channels at the nanoscale for nanofluidics devices. Another domain with potential applications of nano machining includes miniature drug delivery systems.
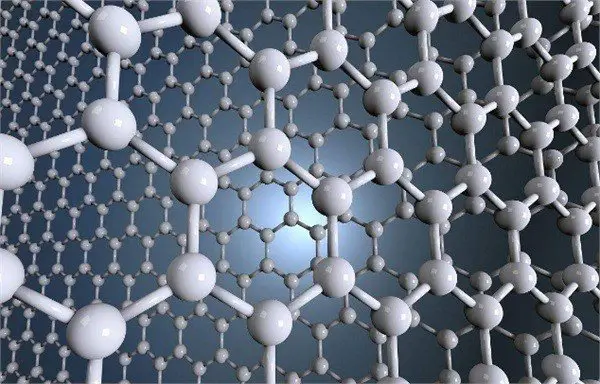
Conclusion
Devices with features having a length scale of a few nanometers are attracting increasing attention from scientists and engineers due to their potential utility in multiple fields such as the food industry, biomedical devices, electronics, mechanics, etc. One of the main hindrances being faced by designers and developers of such devices is regarding their manufacturability. Body of knowledge concerning nano machining is helping scientists and engineers to make progress in manufacturing such devices. Molecular Dynamics Simulation (MDS) provides necessary information regarding important nano machining factors such as cutting force, cutting temperature, cutting energy, chip thickness, and many other related parameters. To achieve precision at the nanoscale level, it is important to select ultra-precision machine tools along with ultra-precision cutting tools. Having the ability to measure and examine produced nanoscale features helps in ensuring quality parts that pass functional testing.