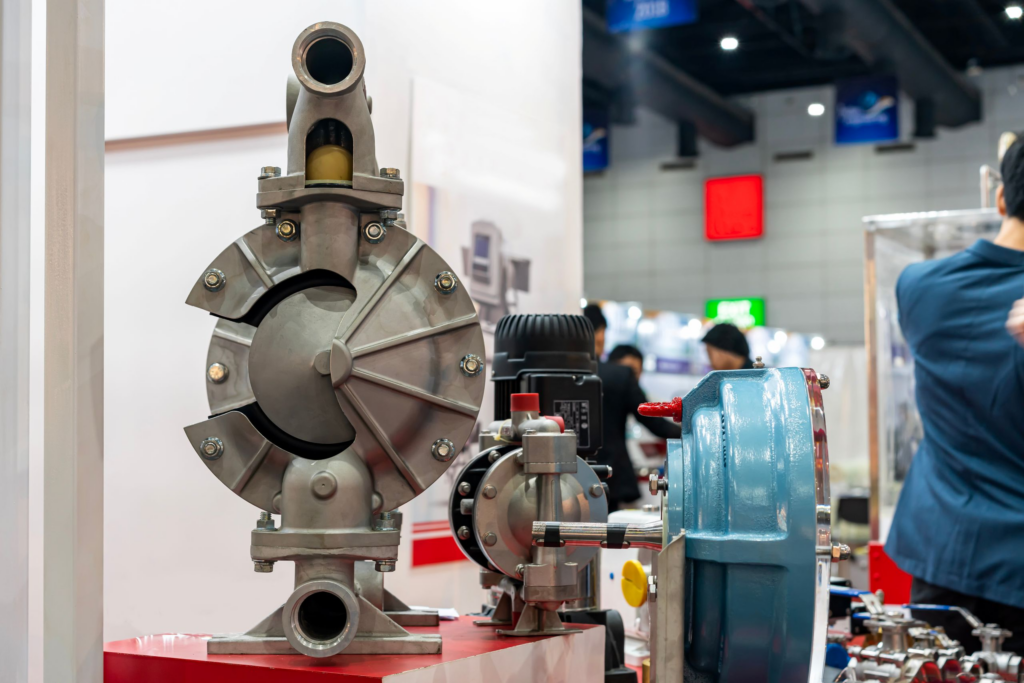
Chemical processing facilities routinely manage a variety of hazardous materials, including corrosive, toxic, and highly flammable substances. Maintaining safety in these facilities is critical—not only for worker protection but also to safeguard equipment and prevent environmental harm. One critical piece of equipment that significantly enhances safety in chemical processing is the double diaphragm pump (DDP). These pumps offer unique advantages that minimize risks associated with leaks, contamination, and mechanical failures.
This article explores how double diaphragm pumps improve safety in chemical processing by examining their design, operational benefits, and real-world applications.
Leak-Free Operation Prevents Hazardous Exposure
Double diaphragm pumps (DDPs) eliminate leakage risks in chemical processing by replacing traditional failure-prone seals with dual flexible diaphragms. This seal-less design prevents hazardous fluid releases, protecting workers and the environment. If one diaphragm fails, the secondary diaphragm maintains containment while leak sensors provide early warnings.
Unlike conventional pumps, DDPs offer inherent safety when handling toxic, flammable, or volatile chemicals. Their rugged construction resists corrosion while preventing fugitive emissions that violate EPA and OSHA standards. This reduces maintenance exposure and avoids costly spills.
Industries handling dangerous materials—from pharmaceuticals to bulk chemicals—rely on DDPs for reliable containment. Facilities report fewer incidents, lower disposal costs, and improved compliance after switching to diaphragm pump technology, making them a cornerstone of modern process safety. Learn more about the benefits of diaphragm pumps at knf.com/en/uk.
Handling Corrosive and Abrasive Fluids Safely
DDPs excel in handling aggressive chemicals and abrasive slurries that rapidly degrade conventional pumps. Their corrosion-resistant materials (PTFE, polypropylene, specialty alloys) and absence of vulnerable impellers make them ideal for acids, alkalis, and particle-laden fluids. The simple design minimizes wear points that typically fail in harsh environments.
DDPs significantly enhance safety through gradual failure modes rather than sudden breakdowns. With no high-speed components or tight clearances, they withstand abrasive particles that destroy centrifugal pumps. This reduces unplanned downtime and prevents hazardous leaks during operation.
The technology lowers maintenance risks by requiring fewer interventions. Workers benefit from less exposure to dangerous chemicals during repairs, while facilities gain reliable, long-lasting performance in demanding applications—from sulfuric acid transfer to mining slurry processing.
Dry-Run and Deadhead Capabilities Prevent Catastrophic Failures
Double diaphragm pumps (DDPs) eliminate dry-run and deadhead risks that damage conventional pumps. Their air-operated design allows dry running without overheating, while automatic pressure balancing prevents dangerous buildup when discharge lines clog. This inherent protection is vital for flammable or heat-sensitive chemicals where thermal events could be catastrophic.
Unlike pumps requiring complex safeguards, DDPs provide passive safety through simple mechanics. The diaphragms stop moving when blocked, avoiding pressure spikes that rupture pipes. Optional relief valves and regulators add extra protection layers for critical applications, making them ideal for automated or unattended systems.
These features prevent seal failures, fires, and unplanned downtime. Facilities handling solvents, polymers, or batch processes benefit from DDPs’ ability to withstand intermittent flow and accidental blockages safely.
Explosion-Proof and Spark-Free Operation
DDPs provide explosion-proof safety in hazardous areas through air-powered operation, eliminating electrical ignition risks. Their non-sparking construction and optional conductive materials prevent static buildup, complying with ATEX and NFPA standards for explosive atmospheres. This makes them ideal for handling volatile solvents and combustible liquids where even minor sparks could trigger disasters.
Unlike motor-driven pumps, DDPs contain no rotating metal parts or hot surfaces that could ignite flammable vapors. Pneumatic models operate safely in Zone 0/1 classified areas without expensive explosion-proof enclosures. Facilities handling fuels, paints, or chemicals benefit from their reliable, spark-free performance.
The combination of certified designs and passive safety features reduces explosion risks while lowering compliance costs. From petroleum terminals to pharmaceutical plants, DDPs offer unmatched protection when processing flammable materials, preventing catastrophic incidents through intelligent engineering rather than added safeguards.
Reduced Noise and Vibration for Worker Safety
DDPs significantly reduce workplace noise and vibration hazards compared to traditional pumps. Their slow reciprocating action (under 100 cycles/minute) generates less sound than high-speed centrifugal pumps, with air-operated models typically producing only 75-82 dBA – below OSHA’s 85 dBA action level. This helps prevent noise-induced hearing loss while often eliminating mandatory hearing protection requirements.
The pumps’ unique design dampens vibrations at their source. Flexible diaphragms absorb pulsations instead of transmitting them through pipes, reducing fatigue and musculoskeletal risks for maintenance crews. Workers report less physical strain during repairs thanks to lightweight components and accessible designs.
By combining low-noise operation with vibration-free performance, DDPs create healthier work environments. Facilities report measurable improvements – from 40% fewer vibration-related pipe failures to faster maintenance times – proving that safer equipment design directly benefits both worker wellbeing and operational efficiency.
Easy Maintenance Without Specialized Tools
Complex pump systems often require skilled technicians and extensive downtime for repairs, increasing worker exposure to hazardous conditions. However, DDPs simplify maintenance in several ways. Their modular design allows for a quick diaphragm or valve replacement without dismantling the entire pump.
Unlike centrifugal pumps, DDPs don’t require precise shaft alignment, reducing installation and repair complexity. Additionally, they have minimal lubrication requirements due to fewer moving parts, which also helps prevent contamination of process fluids. This makes DDPs a more efficient and safer choice for industrial applications.
Compliance with Industry Safety Standards
Regulatory bodies such as OSHA, EPA, and ATEX impose strict guidelines on chemical handling equipment to ensure workplace safety and environmental protection. DDPs are designed to meet these compliance requirements effectively. Its operation minimizes fugitive emissions in accordance with the Clean Air Act.
Many DDP models also carry ATEX certification, making them safe for use in explosive atmospheres. Additionally, for industries requiring stringent hygiene standards—such as food and pharmaceuticals—FDA-compliant DDPs are available, featuring sanitary designs and non-toxic materials to prevent contamination. This makes DDPs a reliable choice for maintaining compliance across diverse industrial applications.
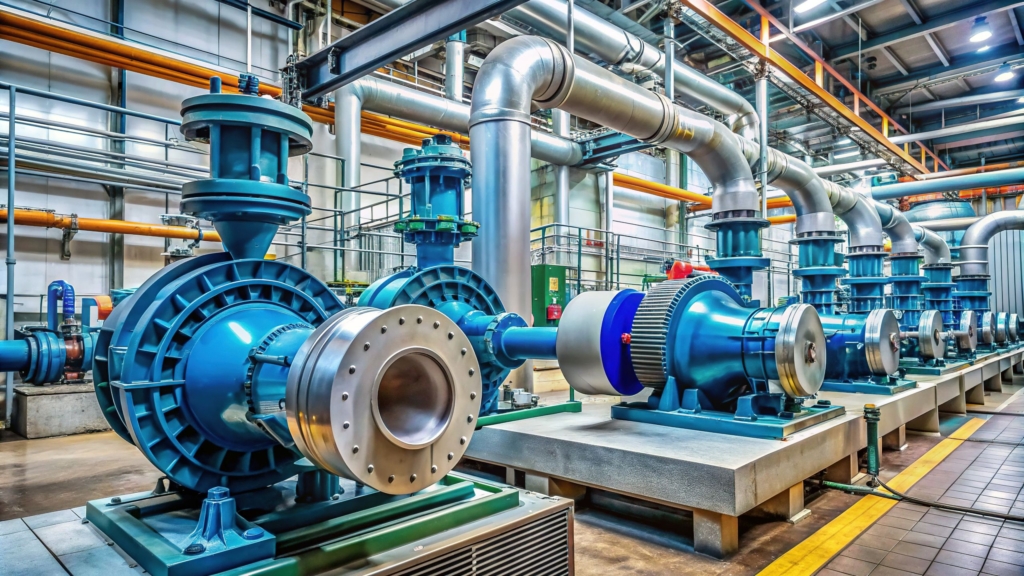
Frequently Asked Questions (FAQs)
1. How do double diaphragm pumps enhance safety in chemical transfer applications?
Double diaphragm pumps are designed with flap valves and check valves to prevent backflow, ensuring safe handling of hazardous chemicals. Their seal-less design eliminates leakage risks, while genuine accessories and air valves enhance critical reliability in aggressive environments.
2. What types of chemicals can double diaphragm pumps handle?
DDPs accommodate a wide range of chemicals, from corrosive acids to viscous solvents. Proper pump material selection, guided by pump experts, ensures compatibility with different ranges of materials, including abrasive or high-temperature fluids.
3. How do double diaphragm pumps achieve superior performance in dewatering and filtration applications?
Their ability to handle size solids and self-prime efficiently makes them ideal for fluid transfer applications, including filtration applications. The suction port and discharge valve ball design ensures smooth inlet to discharge flow, maintaining performance in dewatering even with challenging fluids.
4. Why is material selection crucial for chemical transfer pumps?
A guide for pump material helps choose diaphragms and wetted parts resistant to chemical attack. Leading manufacturers offer options like PTFE, ensuring level of performance and longevity in harsh conditions.
Bottom Line
Double diaphragm pumps can handle corrosive and abrasive fluids, and resistance to dry-running and deadhead conditions makes them a reliable choice for hazardous applications. Additionally, a DDP’s explosion-proof capabilities reduce noise levels, and its ease of maintenance contributes to a safer working environment. Investing in double diaphragm pumps is a proactive step toward minimizing risks and improving efficiency in chemical handling processes.