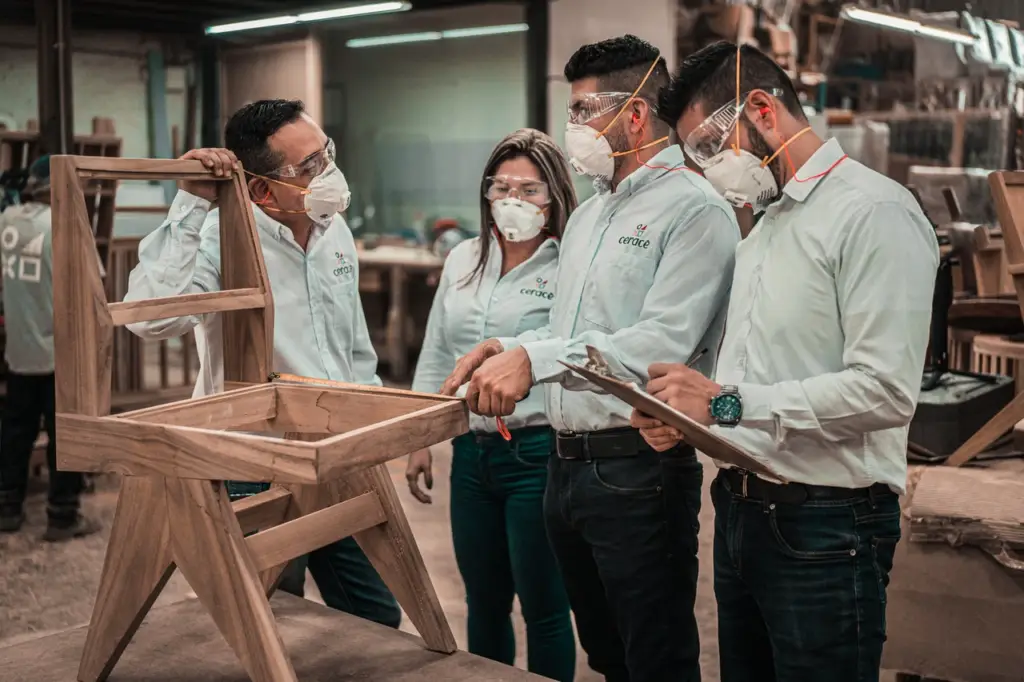
If there’s one thing the current health crisis has taught employers, it’s the fact that they need to invest more time and money in employee safety.
Apart from the threat of disease, companies should also be wary of other risks that require the need of an effective workplace safety program. This is not only essential from a legal perspective, but it is also a moral responsibility that employers will need to assume in order to maintain a good reputation.
No matter the nature of your business, the risk of injury and chronic illness is certain. Fortunately, you can mitigate and reduce the impact of these situations by implementing the right safety measures. Here are some of the best practices you will need to follow:
1. Do a safety assessment
Before you can even implement the right systems and measures for ensuring workplace safety, it’s important to conduct an onsite evaluation. Through a safety assessment conducted by a third-party safety auditor, you will know what your company lacks in terms of facilities, tools, and policies. That way, you can maximize available time and resources for improving safety.
2. Identify hazards and appropriate mitigating measures
During the assessment, pay close attention to structural and environmental factors that expose employees to high levels of risk. Everything from dilapidated ceilings to high concentrations of asbestos should be taken into account. From there, you can work with your onsite safety team to identify what needs to be done in order to reduce the impact of these hazards.
3. Get advice from an occupational clinician
An occupational clinician is a medical practitioner that specializes in evaluating and treating certain diseases in the workplace. They will provide you with insights for preventing health hazards that reduce productivity and eat into the bottom line. With an experienced occupational clinician in your team, you can create a work environment that addresses stress and burnout, improves work-life balance, and reduces the risk of injury and chronic illness using evidence-based approaches.
4. Spend on improvements that add long term value
Once you have a good idea of the hazards your employees are facing, you should be able to spend on improvements that can last a long time. It won’t help to settle for band-aid solutions that work only for the short term. If you are looking to improve air quality in your industrial worksite, for instance, setting up a basic HVAC system isn’t enough. You are better off installing advanced ventilation systems through companies like RoboVent to prevent the buildup of dust and other debris. You may have to spend a lot of money for such improvements, but it’s far better than having to deal with an onsite injury or illness.
5. Get your employees involved
Workplace safety is not just the responsibility of the management. Everyone has a role to fill in creating a hazard-free work environment. Consider reaching out to your employees and asking for their inputs. You can also encourage them to call out any potential workplace hazards they see and take part in drafting safety protocols.
Each year, companies and individuals spend billions of dollars to deal with the consequences of workplace hazards. It would be more practical to mitigate these risks, so start by following the best practices above and improve your business’s safety factor.