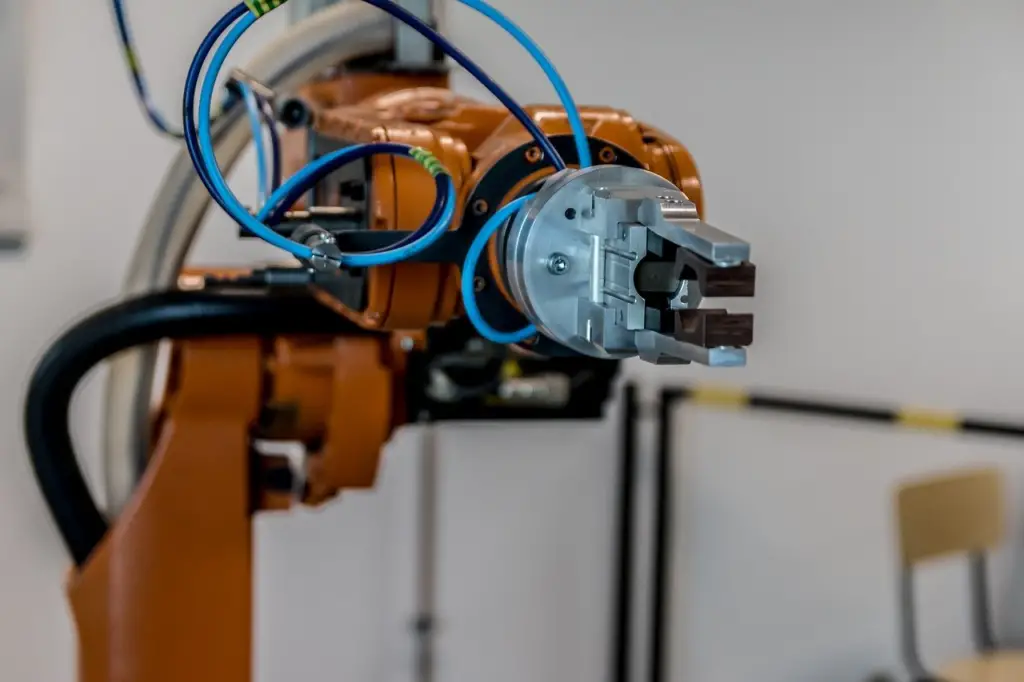
Manufacturing industries churn out products that are then polished to achieve a high-quality, smooth, and shiny finish. Due to high volumes of production, manual polishing lags the whole process. Robot automated systems have revolutionized manufacturing by saving time and costs while maintaining consistency in polishing tasks.
Robots are radically changing the way polishing is carried out. From the advent of painting, most of the techniques have been achieved by hand.
Automated polishing took over high-volume works and handled complex shaped parts. Still more complex parts provided polishing challenges, and polishing remained a hand operation where people had to manipulate elements to complete the required finishing.
The entry of robotics led to the automation of complex and straightforward finishing applications and opened the door for robot polishing. By replicating the motions of humans during the finishing process, robots present an effective polishing system achieved through a programmed repetitive path.
Robot polishing became an ideal choice for sealant dispensing, spray painting, and finishing. Moreover, robots with their six axes of motion can maneuver complex shaped parts.
Industrial Applications of Robot Finishing
Buffing and polishing are two terms that are common in a manufacturing setup and are applied in adding an aesthetic property to the end products. Buffing is performed after polishing to produce shiny surfaces on wood or metal.
Almost all manufacturing operations require some hand finishing to fine-tune the end product. Here are examples of industries that have successfully automated their hand finishing applications with robotics:
Aerospace: Airframe spars, stringers, combustion housings, skins, engine fan, blade root, and disks.
Domestic: pots, pans, knives, forks, lamp bases, vacuum cleaner trim, sinks, faucets, bases, and handles.
Marine: Deck hardware propellers, drive housings.
Automotive: Robot polishing is applied in finishing Trim components, fenders, engine transmission, plastic trim, motorcycles suspension, gas tanks, and bumpers.
Hardware tools such as locksets, knobs, levers, hinges, and trim components are beneficiaries of robotic finishing. Medical implant instruments such as knees, and hips are results of robot automated systems.
Factors to Consider Before Introducing Robotic Polishing
Labor Cost
It is paramount to consider the hand polishing rates and the number of workers per shift for comparison purposes.
Workers Compensation Cost
In line with the health and safety requirements, the introduction of robots brings in benefits. Such benefits include minimizing risks of operation such as exposure to noisy and dirty environments.
Communicating Benefits to the Employees
Like in any change process, there must be some amount of resistance. As such, it is paramount to educate staff on the benefits of the robot while assuring them there will be no job losses but only reassignments.
Whether the Project is Well Defined
Here, the managers address current organizational problems to be solved through automation. Such issues include labor costs, work-based injuries, quality, and capacity. By assessing the problems staff can fully appreciate the benefits of automation.
Advantages of Robot Polishing
Robots ensure consistency when polishing and buffing and can produce the same results on curved and uneven surfaces. Robotics are forcible and can easily adjust their inclination to achieve the desired task.
Furthermore, robots take care of health and safety by handling dangerous tasks in risky places, thus relieving humans from working in unsafe areas. Robots can remove excess particles and maintain uniform and consistent polishing.
Robots handle volumes of tasks with ease and decrease manual labor, thus saving time and money. They work long hours on end without showing signs of fatigue. Their turnaround time is impressive.
The introduction of polishing robots in a factory setting increased the production capacity, reduces workers, and save costs and wastages. Since robots are programmed to precision, wastages are minimized.
As opposed to common beliefs that robot automation leads to job losses, it, in fact as facilitates better use of the workforce; it allows management to reassign the finishing staff to other productive tasks.
Robotics reduces the energy levels consumed in the organization. The reduction is achieved through programming robots to attain optimum energy levels. Their movements can be limited to necessary moves only.
Manual Vs. Robotic Polishing
Manual polishing is labor-intensive, thus costly as a person will clock several hours smoothing surfaces with coarse adhesive before employing fine abrasive. As such, it is tedious for massive projects.
On the other hand, robot polishing is suitable for large projects and best suits manufacturing industries such as automobile, medical, marine, gaming, aerospace, and many others that require mass polishing of metallic objects.
Robots can smoothen rough surfaces and grind parts to achieve consistent finishing. Manual polishing, on the other hand, is suitable for fine-tuning complex symmetrical specifications.
Robot polishing utilizes less labor and time. There is no rest, breaks, or sleep. They can work long hours on end until the completion of the task. Humans need a rest, lunch breaks, and work in shifts hence consume more time.
Humans can waste the abrasive materials used for sanding by inconsistently using them. The manual process wears polishing tools. Programmed robots cut wattage to minimum levels and can adjust their operation to minimize tool wear. By adjusting their tools, robots ensure an extended tool life.
Conclusion
Robot polishing is gaining popularity fast, and its benefits outweigh manual polishing. Any company, whether big or small, can use robots to improve their polishing tasks. Manufacturers are using polishing robots to achieve consistent qualities on surface finishes.
In large production areas, robot polishing is programmed to complete a particular task and replicates the same process without human boredom. In essence, metal polishing is repetitive and tedious and is best left to automated robots.
Robot polishing brought about the much-needed consistency and avoided variability witnessed in hand polishing operations. It should bed noted that polishing requires grinding, finishing, recurring, and polishing. Hence achieving a polished surface is a thorough process that is time-consuming and labor-intensive. The robotic process reduces the cycle time and improves productivity.
Nevertheless, robot polishing does not entirely cast an end to hand polishing. Manual polishing is needed to finish part-to-part and involve geometric definitions that the robot may not understand. Therefore, hand and robot polishing need one another.