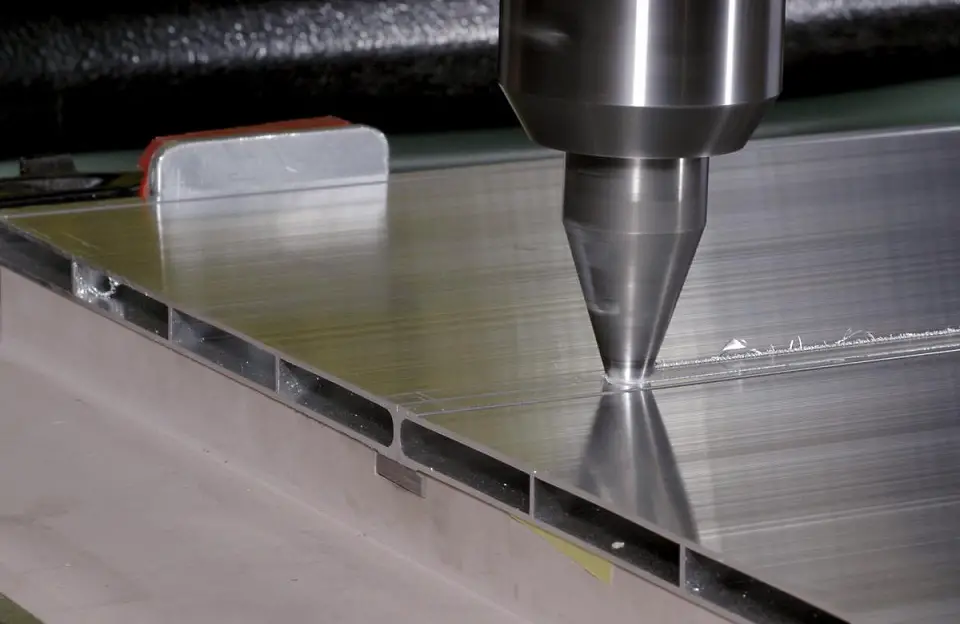
All industries today try to be environmentally conscious. It is also the case when welding is called upon, in various industries. FSW (Friction Stir Welding) does not need as much energy and generates no gas, two ecological qualities it delivers, upon others. Below, you will discover what this welding method offers in terms of qualities, benefits and what it is used for.
The Qualities of Friction Stir Welding
To understand the qualities this method offers, you have to compare it to traditional welding techniques. Whereas the other ones need filler material, gas and other consumables, FSW does not require any of them. Friction stir welding is also much better for the environment people work in, as it makes a very little sound, and generates no slag or spatter, nor does it release any gas. But the two most important qualities, for those using it, is that it produces high-quality work and it helps to increase productivity.
Because of all these characteristics, FSW has created new opportunities in the world of welding technology. It can now weld together pieces of aluminum, copper and magnesium; something traditional welding cannot do.
The Key Benefits of FSW
Moving away from traditional welding to friction stir welding comes with many advantages. One of the most important is that once the welding is done, the mechanical properties of the metal are still intact. That is very useful and uncommon. Working with welding can cause a lot of residues around the workspace and create unwanted fumes. It is not so when you use FSW. It also completely reduces the risk of getting hurt while welding.
When a welder uses another technique, he may not be able to work in the position he would like. With friction stir welding, placing the object horizontally or vertically, will not be a problem. Also, the person in charge does not have to clean the metal sheet first or to treat it in any particular way afterward, either.
Its Applications
There are many industries that have benefited already from these welding techniques. Amongst them, let’s mention: Aerospace, automotive, railway, transportation, naval industry, heat transfer and nuclear. It has helped particularly in the fabrication of aluminum products. For example, the railways use it to produce prefabricated aluminum panels, while the automotive industry uses it for parts they often need, such as alloy wheels and fuel tanks.
Friction Stir Welding has now been around for over 25 years, having first been patented in 1996. Its capacities to join aluminum to other metals will enable it to have a great impact on many industries.