Seamless stainless steel pipes are essential in industries that demand reliable, quality materials for critical functions. These pipes, formed without a welded seam, are preferred for their uniform structure, high-pressure resistance, and durability under challenging conditions. However, creating pipes that meet rigorous industry standards is a precise process that relies on systematic testing and quality control at each stage.
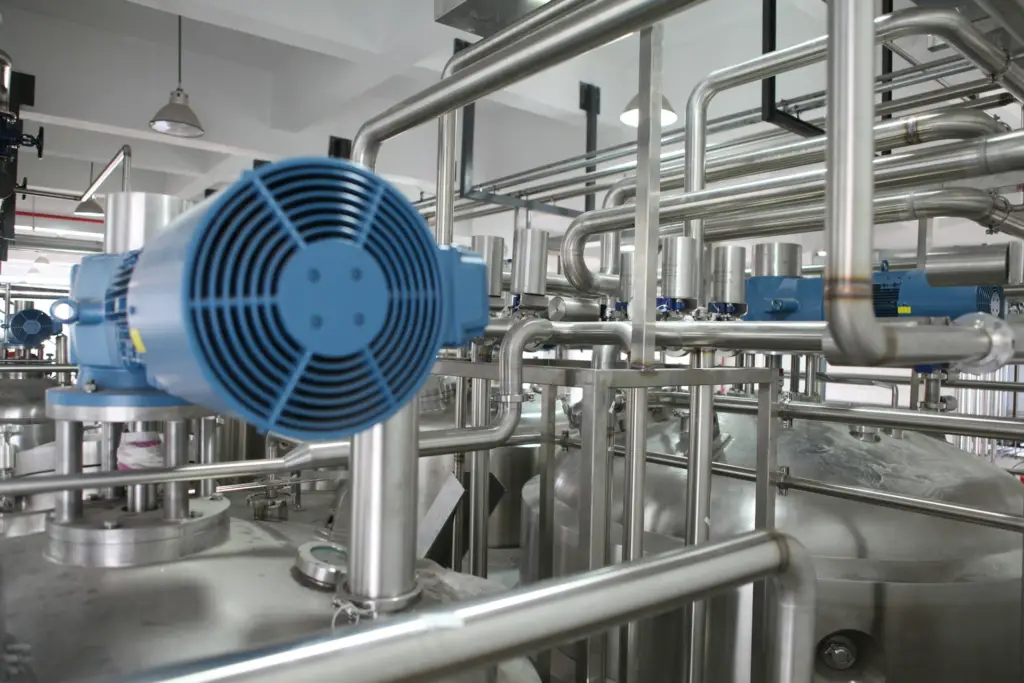
Let’s explore the specific testing methods and quality control practices in seamless stainless steel pipe production, breaking down how each contributes to product reliability, compliance, and safety.
Why Quality Control Matters in Pipe Production
Quality control in seamless stainless steel pipes production is not just about meeting industry standards; it’s about ensuring pipes can withstand the stress, temperature, and pressure variations they will encounter. A robust quality control program:
- Reduces risk of failure: High-quality pipes help prevent breakdowns, leaks, and operational disruptions.
- Meets industry compliance: Regulatory bodies have strict guidelines for pipes used in the construction, manufacturing, and energy sectors.
- Builds customer trust: Consistent quality ensures that buyers receive a product they can rely on, even in high-stakes applications.
For seamless stainless steel pipes, quality control goes beyond surface inspections. It requires comprehensive testing from start to finish to ensure pipes are structurally sound and free from flaws.
Core Stages in Quality Control for Seamless Pipes
The production of seamless stainless steel pipes involves several key stages, each with specific quality control requirements. Here’s a closer look at how each stage is managed to ensure quality and consistency.
1. Raw Material Selection and Inspection
Quality control begins with the raw material itself. Manufacturers select high-grade stainless steel billets, which are then inspected for chemical composition and physical defects.
The right balance of elements, such as chromium and nickel, gives stainless steel its corrosion resistance and strength. Accurate composition is essential for maintaining these qualities. A physical inspection for surface cracks or impurities helps identify potential weak spots early so they don’t carry through to the final product.
2. Heating and Piercing
After selection, billets are heated and pierced to form the hollow structure that will become the pipe. Quality control at this stage focuses on precision and consistency.
- Temperature monitoring: Controlling the heat level is critical to ensure uniformity in the steel’s properties. Too high or too low, and the steel may not form correctly.
- Piercing checks: Proper alignment and pressure during piercing are essential to prevent the formation of irregularities inside the pipe.
3. Rolling and Sizing
Once pierced, the pipe goes through a series of rolling and sizing processes to achieve the desired thickness and diameter. This stage is heavily quality-controlled to ensure uniform dimensions and surface quality.
- Dimensional accuracy testing: The diameter and wall thickness are measured to ensure they meet the required tolerances.
- Surface inspection: Any remaining surface irregularities are identified and corrected at this stage, ensuring the pipe has a consistent, smooth surface.
Testing Methods in Seamless Stainless Steel Pipe Production
Testing is a core part of quality control, verifying that each pipe meets structural and material standards. The main methods used in seamless pipe testing fall into two categories: non-destructive and destructive testing.
Non-Destructive Testing (NDT)
Non-destructive testing is used to evaluate the pipe’s integrity without causing any damage. This type of testing is especially important for detecting internal flaws that might not be visible on the surface.
Ultrasonic Testing (UT)
Ultrasonic testing uses high-frequency sound waves to detect internal cracks, voids, and inclusions. It can locate subsurface flaws that could weaken the pipe. It’s a standard technique in the industry because it provides reliable results along the entire length of the pipe. High-frequency sound waves are sent through the pipe. When they hit a flaw, they create an echo that is measured and analyzed.
Eddy Current Testing (ECT)
Eddy current testing is another non-destructive method, using electromagnetic induction to detect surface and near-surface defects. It is fast and can inspect large volumes of pipes, making it suitable for ongoing quality checks.
Magnetic Particle Testing (MPT)
Magnetic particle testing involves applying a magnetic field to the pipe and then using iron particles to reveal cracks. MPT is effective for finding surface-level flaws that may compromise the pipe’s durability. It’s a quick and reliable method that gives immediate feedback.
Destructive Testing
Unlike non-destructive methods, destructive testing involves physically stressing the material to its limits. While it sacrifices the tested piece, it provides invaluable information on material performance.
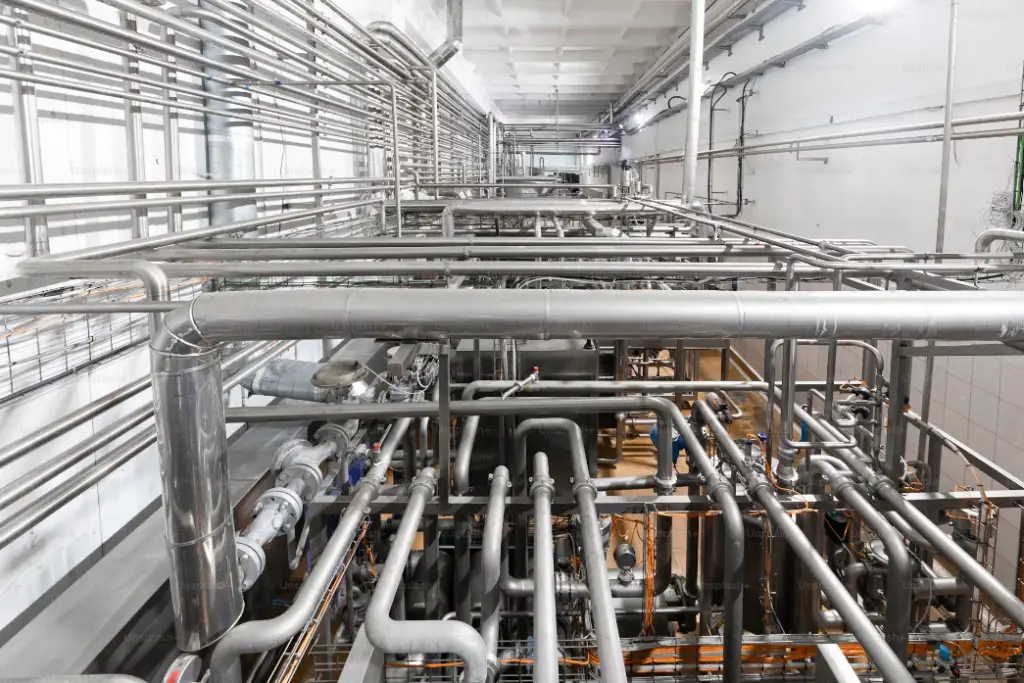
Tensile Testing
Tensile testing measures how much force the pipe can withstand before it breaks. Key results include:
- Ultimate Tensile Strength (UTS): The maximum force before failure, indicating how much load the pipe can bear.
- Yield strength: The stress level at which the pipe deforms permanently, which is critical for applications requiring flexibility without compromising strength.
Hardness Testing
Hardness testing determines the material’s resistance to wear and deformation. This test can give insight into how well the pipe will handle abrasive environments or high-impact conditions. Rockwell and Brinell are common hardness tests, which press a metal ball or cone into the surface and measure resistance.
Impact Testing
Impact testing evaluates how well the pipe can absorb energy in sudden, forceful situations, such as accidental impacts. It is essential for pipes used in cold environments, as brittleness can increase at lower temperatures.
Advanced Quality Control Techniques
X-ray scanning can reveal internal flaws that even ultrasonic testing might miss, offering a deeper view into the pipe’s structure. For applications that require precision, laser scanning provides a detailed measurement of dimensions down to the smallest variations. During production, thermal imaging can identify inconsistencies in heat distribution, which might indicate areas of the pipe that are less structurally sound.
Quality Control as a Core Principle
Testing and quality control in seamless stainless steel pipe production aren’t just added steps; they are the foundation that ensures reliability, compliance, and safety. The commitment to thorough quality control is what makes seamless stainless steel pipes trusted components in applications that require nothing less than absolute reliability.