Did you know that 82% of companies experience unexpected downtime because they don’t catch equipment-related issues in time? If you’ve ever faced this problem, you know how frustrating and expensive it can be.
Equipment monitoring is needed as it helps you detect issues early before they spiral into major breakdowns. However, even the best systems can fall short if certain mistakes are made. In this article, we’ll discuss common equipment monitoring mistakes you might make and how to avoid them.
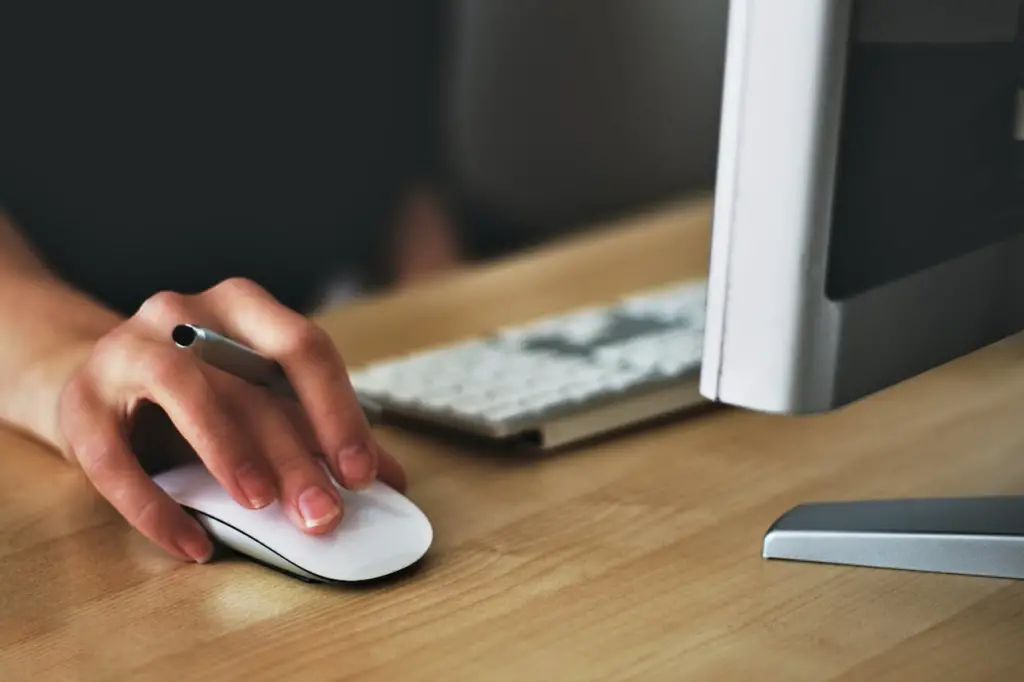
Not Setting Clear Monitoring Goals
It’s easy to assume that installing equipment monitoring tools will automatically improve performance. But here’s the thing: the data won’t be as helpful if you don’t know exactly what you’re monitoring for. Think about it like driving a car without a destination. You’re moving, but are you getting where you need to go?
How to Avoid This Mistake: Start by identifying your goals. Do you want to reduce maintenance costs, increase equipment lifespan, or prevent unplanned downtime? When you know what you’re aiming for, you can set up your system to track the right data and focus on what matters most to your business.
Relying Only on Reactive Maintenance
When you only react to problems as they occur, you’re constantly putting out fires instead of preventing them. If your equipment breaks down and your first step is to fix it after the fact, you’re losing valuable time and money.
How to Avoid This Mistake: Shift your focus to preventative maintenance. Use your monitoring system to spot early warning signs, like unusual vibrations or temperature spikes, so you can address small issues before they turn into big, costly repairs.
Not Analyzing the Data Regularly
Having a monitoring system is great, but you’re missing out on valuable insights if you don’t regularly review the data. It’s easy to get busy with day-to-day operations and overlook the reports that could be telling you something important.
How to Avoid This Mistake: Check your equipment data regularly. Set up automated alerts for significant changes and schedule time to analyze the reports at least weekly. This way, you can stay on top of any developing issues and spot trends affecting your equipment’s long-term performance.
Ignoring Small, Repeated Issues
Let’s say your equipment starts making a strange noise or running slightly slower than usual. Ignoring these minor issues is tempting because they don’t seem urgent. But these small problems often signal larger issues brewing beneath the surface.
How to Avoid This Mistake: Take every irregularity seriously. Your monitoring system is there to pick up on these early signs of trouble. If something seems off, investigate it right away. A quick fix now can save you from an expensive repair down the road.
Overloading the Monitoring System with Too Much Data
While it’s great to collect data, there’s such a thing as too much data. If you’re monitoring everything under the sun, knowing what’s actually important becomes difficult. You get overwhelmed with information, and the key issues can get lost in the noise.
How to Avoid This Mistake: Focus on your specific equipment’s most critical data points. Monitor metrics like temperature, vibration, pressure, and energy use, but only if they are relevant to your goals.
Not Training Your Team on the System
You’ve invested in the best equipment monitoring system, but your team isn’t familiar with it. It can lead to missed alerts, overlooked data, and incorrect interpretations. If your team doesn’t fully understand the system, you’re not getting the full benefit of your investment.
How to Avoid This Mistake: Make sure everyone understands how to read the data, respond to alerts, and perform basic troubleshooting to solve basic problems. The more comfortable your team is with the system, the more smoothly your operations will run.
Not Involving Your Team in the Monitoring Process
It is easy to leave the monitoring process to the IT or maintenance departments, but your entire team keeps equipment in top shape. Operators, for example, often have the closest eye on the machinery and can notice things the monitoring system might not pick up on.
How to Avoid This Mistake: Encourage open communication between departments. Train your equipment operators to report unusual behaviors or minor issues they notice during their shifts. When everyone is involved, you’ll catch issues faster and keep equipment running at its best.
Conclusion
Equipment monitoring can save you time, money, and stress, but only if you use it effectively. It’s all about being proactive and staying ahead of potential issues. When you take a hands-on approach to monitoring, you’ll keep your operations running smoothly and avoid unnecessary headaches. Ready to get more out of your equipment monitoring system? The effort you put in now will pay off with fewer breakdowns, lower maintenance costs, and better overall performance.